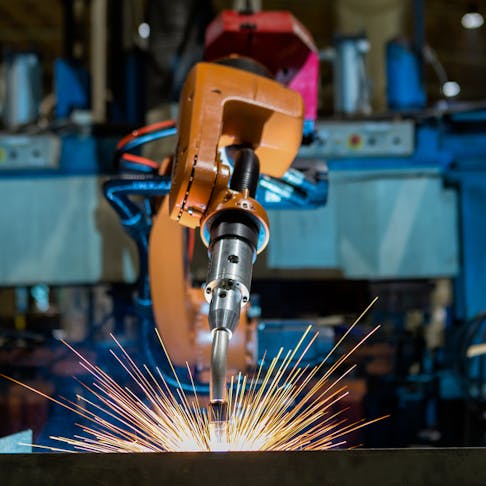
Laser Welding vs MIG Welding: Understanding the Basics
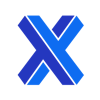
Welding is a process that uses a high energy source and localized heating to fuse two or more generally similar/identical materials together to make a native material junction with the best possible properties. A range of methods has been developed, with an increasing focus on electric arc systems. The majority of these use a continuous consumption of filler wire to assist the fusion and to deliver the arc from a sacrificial tip.
MIG (metal inert gas) welding uses an inert gas shield and a continuous feed of filler wire as the electrode. Laser welding is closely parallel, though the energy for melt/fusion is a focused, coherent light beam. A similar gas shield is required. Laser welding works well without filler rods, where joint geometry and material properties allow.
What Is Laser Welding?
Laser welding is a jointing process that utilizes a laser beam as the heat source to melt and fuse together similar and potentially dissimilar materials. It is a precise and highly controlled technique that has advantages over other techniques when the process is suitable. However, it carries a burden of equipment costs, specialist knowledge, and safety considerations.
The focused laser beam provides the energy for melting/fusion. Fiber or CO2 lasers are the typical primary energy source, transmitted to the point of application via mirrors or optical fibers. Laser welding of two main types can be carried out: conduction mode welding for thin materials and surface coupling, and keyhole welding for deeper penetration into the joint. The technique is adaptable to the jointing of a surprising range of substrate materials. This technology enables control of the heat input and weld parameters. Close focus provides for highly localized heating and minimized heat-affected zones (HAZ). This can result in low distortion and applicability to extremely fine work. Laser welding can also be fast. The high effective power/area of the laser enables rapid melting at a limited size spot, resulting in short welding cycles. It is relatively easily integrated into automated manufacturing processes. It is highly compatible with robotics/automation, enabling complex welds with extreme repeatability and precision.
How Does a Laser Welding Work?
Laser welding functions by the application of a highly focused, collimated, and narrow beam of radiation to induce heating to melt and fuse components. It is suited to very small and controlled welds but adaptable to larger work. Listed below are the basic steps in laser welding:
- Prepare the materials to be welded by cleaning and aligning the junctions to ensure precise contact. These surfaces may also be preheated or coated with an oxidation-suppressing material.
- An appropriate coherent energy source, usually a fiber or CO2 laser, emits a high-energy beam. The energy beam is generated by stimulated emission in the lasing medium.
- The emitted beam passes through a delivery path of mirrors or light pipes to a series of lenses, to focus it into a spot, achieving high specific energy (energy concentration per unit area).
- The beam delivery optics deliver the radiation to the weld commencement location.
- As the focused laser energy impacts the workpieces, localized heating and rapid melting of the joint area results.
- As the material liquefies, the molten pool fuses the joint areas of all parts. The edge of the melt pool is extended along the junction, and as the point of laser application advances, the trailing edge of the melt pool rapidly cools.
- The solidified material forms a weld bead, which merges the workpieces. If unlike materials are joined by a more asymmetric application of heat, the joint properties should be considered representative of the weakest material present.
How Important Is a Laser Welding?
Laser welding plays a critical role in a wide range of applications and manufacturing processes, delivering one or several of the significant advantages listed below:
- Laser welding achieves exceptional precision and control when expertly set up. The process is highly accurate, producing minimal HAZ/distortion, precise weld profiles, and precision in welded joints.
- The approach is versatile and applicable to many materials, including metals, alloys, plastics, composites, and ceramics. Joining dissimilar materials with divergent melting points allows for high-strength and low-design-constraint junctions.
- The process is fast and efficient when established by capable technicians, with shorter cycle times than comparable methods.
- The low heat and debris nature of the process allows for clean and simple integration into automated and robotic manufacturing. Optical systems for rapidly adaptive welding of complex joints allow substitution for much more complex processes.
- Laser welding is particularly suitable for fusing delicate materials and components. Its non-contact nature and controlled heat minimize collateral damage. This makes laser welding ideal for applications in the electronics, medical, and jewelry industries.
This approach to welding enables great flexibility in joint design and weld configuration. This facilitates flexibility that enables innovative product designs and simplifies assembly processes.
What Is the Purpose of Laser Welding?
As with all welding methods, the purpose of laser welding is to join two or more materials together. Laser welding offers advantages over established methods and serves across different industries, including:
- Joining similar, dissimilar, and even “incompatible” materials.
- Precise and high-quality welding and otherwise near-impossible micro-welding.
- Small heat-affected zone.
- High processing speed/productivity.
- Highly amenable to automation and machine integration.
- Versatile and flexible process.
- Non-contact and low collateral damage, due to tightly controlled energy application and near zero “exhaust” or splash.
What Are the Uses of Laser Welding?
Laser welding finds application across diverse sectors in both value proposition and scale, including:
- Automotive Industry: Used for attaching body panels, assembling monocoque structures, constructing systems, and sealing fuel tanks.
- Aerospace Sector: Crucial for high-strength and high-stress-distribution joining of all aircraft components.
- Medical Equipment and Implants: Useful in the manufacture of medical devices such as implants, surgical instruments, and diagnostic equipment.
- Electronics Manufacturing: Used in the electronics industry for low-disruption jointing of components such as connectors, batteries, sensors, and microelectronics.
- Jewelry Making: Used in the jewelry sector for effecting near-invisible joining of precious metals.
- Tool and Die Manufacturing: The process is heavily utilized in tool and die manufacturing for repairing and modifying plastic mold tools, metal casting dies, and other tooling components.
- Energy Sector: Heavier-grade laser welding is used in the energy production sector. It serves in welding components of turbines, boilers, pipelines, and other energy infrastructure.
What Are the Advantages of Laser Welding?
Laser welding offers various clear advantages over traditional gas, electric arc, and chemical welding methods, including:
- Precise and Tightly Controlled Processing: The laser can be finely focused, allowing for finely localized and intense heating, giving precise control of the weld depth and width.
- Weld Quality: Laser welding, when well executed, produces joints with native material strength, good integrity, no inclusions or porosity, and less need for post-weld improvement.
- Versatile Material Range: The technology is compatible with the widest spectrum of materials of any welding method. Enabling the welding of dissimilar materials has created potential in jointing materials/pairings that are otherwise impossible to weld.
- Speed and Cost Benefit: Laser welding is operationally quick and highly efficient, contributing to increased productivity and reduced manufacturing costs.
- Non-contact Welding: Since no hardware ever touches the materials being welded, there is no risk of contamination or damage to the weld area or equipment.
- Automation and System Integration: Laser welding modules are amenable to being integrated into manufacturing systems.
- Design Flexibility: Alleviating the difficulties of other jointing systems, designers are free to solve development issues with fewer constraints.
What Are the Disadvantages of Laser Welding?
Listed below are the limitations and disadvantages of laser welding:
- CAPEX (Capital Expenditure) Cost: The initial cost of laser welding equipment and its implementation is typically higher than most other welding/jointing methods that might be employed in its place.
- Specialized Knowledge and Expertise: Requires extensive training and experience to operate and maintain the equipment to deliver quality outcomes.
- Sensitivity to Joint Separation: The process is very sensitive to joint tolerances, alignment, and fit between the parts, particularly if filler materials are not utilized. Misalignment or poor fit leads to weld defects, reduced strength, and porosity.
- Limited Joint Thickness: Laser welding is best suited to lighter materials. While advancements in laser technology have increased its capability to weld thicker materials, there are limitations compared to some traditional welding methods.
- Susceptibility to Surface Condition: Surface contaminants, such as oil, grease, or oxides will interfere with the welding process and lead to poor weld quality or defects.
- Reflective Materials: Laser radiation can encounter absorption difficulties when working with highly reflective materials, such as stainless steel, aluminum, or copper. This can cause a significant portion of the laser energy to reflect.
- Safety: High-intensity laser beams pose significant safety hazards, which must be reflected in the establishment and operation of the process.
What Is MIG Welding?
Metal inert gas (MIG) welding uses a DC electrode filler wire and an inert gas shield to apply heat to the workpieces. The arc generates intense heat, which liquefies the electrode wire and the workpieces, fusing three or more elements. Power is supplied by a welding machine that integrates various functions such as:
- DC power supply to enable the arc—current controlled to facilitate sufficient power without a disruptive excess.
- Wire feed at a controlled speed, to apply the arc/filler at a rate suited to the task.
- A gas feed shields the melt zone from the atmosphere to prevent oxidation/burning (gas metal arc welding GMAW). Alternatively, flux-cored filler wire releases volatilized shield gas as the arc strikes (flux-cored arc welding FCAW).
- A torch that integrates all the functions and the start/stop control at the point of application.
- A soft start system that allows some degree of gentle initiation of the melt pool at the point of the arc application.
MIG welding is commonly used in industries such as automotive, manufacturing, construction, and general fabrication. It is most applicable to heavier materials, due to the HAZ and distortion.
How Does a MIG Welding Work?
The welding process involves the typical weld stages in forming a strong, high-quality bead that makes the joint, with variations that result from the details of the process:
- Gas, DC arc current, and wire feed are initiated.
- The tip of the wire touches the workpiece, which has been earthed to the welding machine.
- The arc strikes (with or without a soft start) and this immediately creates a melt pool of the filler and the workpiece joint areas close to it.
- The arc increases the local temperature and melts additional filler into the pool.
- An oscillating or rotary motion of the torch extends the melt pool in the direction of the joint and diminishes contact with the trailing edge of the pool.
- The weld advances along the joint line, forming a fused bead of filler that merges into the workpiece(s).
Throughout the MIG welding process, the operator (or more rarely automation system) must maintain close control of the arc power, torch movement pattern, speed, distance from the workpiece, and filler feed rate. These factors dramatically influence the quality and characteristics of the weld joint.
How Important Is a MIG Welding?
MIG welding is a widespread and important welding process that offers significant benefits. It remains the typical welding process for heavier applications including: the production of high-quality welds, versatility, and higher productivity. It is used for joining components, fabricating structures, repairing machinery, and more. MIG welding combines versatility, speed, ease of use, and low operational cost in enabling efficient and reliable welding solutions for a wide range of industries and applications.
What Is the Purpose of MIG Welding?
The purpose of MIG welding is to join metal components together to create a strong and durable weld. High structural integrity, fast processing, and adequate aesthetics result. MIG welding can join like materials, across aluminum alloys, various steels and stainless steels, titanium, and some copper alloys.
What Are the Uses of MIG Welding?
MIG welding has a wide spectrum of applications across various industries, including:
- Automotive Industry: Extensively used in the automotive industry for various applications, including the assembly of car frames, welding body panels, fabrication of exhaust systems, and the repair of vehicle components.
- Manufacturing and Fabrication: Widely employed in manufacturing and fabrication processes. It is used to join metal components in the production of machinery, equipment, appliances, structural steel, furniture, and other fabricated metal products.
- Construction: Plays a vital role in construction projects, such as the fabrication and assembly of steel structures, bridges, pipelines, and architectural metalwork. It is also used for welding reinforcements in concrete structures and for on-site repairs and modifications.
- Shipbuilding and Marine Industry: Used in the shipbuilding and marine industry for welding various components, including ship hulls, decks, bulkheads, pipelines, and other structures. The ability to weld in different positions makes MIG welding suitable for the challenging and complex geometries encountered in shipbuilding.
- Aerospace Industry: Fabrication and repair of aircraft components. It is used for joining structural parts, engine components, fuel tanks, and other critical aircraft assemblies.
- General Metal Fabrication: Widely utilized in general metal fabrication shops for a variety of applications. It is used to create weld joints in sheet metal fabrication, welding of gates and fences, ornamental metalwork, furniture manufacturing, and other custom metal fabrication projects.
- Maintenance and Repair: Employed for maintenance and repair work in various industries. It is used to repair damaged metal parts, perform equipment modifications, fix cracks and breaks, and restore worn-out components.
- DIY and Hobbyist Projects: Accessible to DIY enthusiasts and hobbyists due to its relative ease of use. It is commonly used for personal projects, such as building custom metal structures, creating artwork and sculptures, automotive repairs, and home improvement tasks.
- Pipe Welding: Utilized for welding pipes in industries such as oil & gas, chemical processing, plumbing, and infrastructure development. It is employed for joining pipes made of various materials, including carbon steel, stainless steel, and non-ferrous metals.
- Industrial Manufacturing: Integrated into industrial manufacturing processes in which efficient and reliable welding is required. It is used for assembly line welding, the production of consumer goods, the fabrication of metal components, and various other manufacturing applications.
What Are the Advantages of MIG Welding?
MIG welding offers various advantages that have rendered it the dominant method over other welding processes. These include:
- Ease of Use: MIG welding is relatively easy to learn and execute to a good standard, making it suitable for both beginners and experienced welders.
- High Productivity: It is a fast and low-cost process.
- Versatility: MIG welding is applicable to many metals and a wide spectrum of joint configurations, including all orientations—including overhead.
- Good-Quality Welds: It produces good welds with an acceptable appearance and minimal spatter.
- Continuous Welding: The use of spooled filler wire in MIG welding enables continuous welding without the need to stop and replace electrodes. This reduces downtime and increases overall process efficiency.
- Automation: MIG welding is amenable to automation and can be integrated into robotic systems.
- Cost: It is a cost-effective welding process, compared to other welding methods, and the high productivity and efficiency of the process restrain labor costs.
What Are the Disadvantages of MIG Welding?
While MIG welding has numerous advantages, some disadvantages and considerations must be assessed:
- Limited Outdoor Use: The shielding gas used in the process can be easily disrupted by moving air, which compromises weld quality.
- Equipment Complexity: MIG welding equipment can be relatively complex and requires additional components such as: a power source, wire feeder, gas cylinder, and shielding gas. In particular, torch maintenance is a burden that can take additional “unproductive” time.
- Skill and Technique: While MIG welding is relatively easy to carry out to a basic level, great results demand great skill and experience.
- Limited Penetration: MIG welding is generally better suited for welding thinner materials, typically up to around ½ inch (12.7 mm) thick. Other processes such as standard arc welding offer better options for thicker joints.
- Shielding Gas: Remote welding with poor access to gas services can be challenging, although the use of flux-cored filler wire is a practical option.
- Weld Appearance: Less skilled operators and poor accessibility can produce more spatter compared to other welding processes, resulting in additional cleanup and post-welding work. The weld bead appearance may also require additional cosmetic finishing if a visually appealing weld is necessary.
What Is the Difference in Heat Source Between Laser Welding and MIG Welding?
The heat sources used in laser welding and MIG welding are very different. In laser welding, a focused and coherent beam of infrared laser energy is directed at the workpiece(s). The laser beam from a solid-state, fiber, or CO2 laser is directed at the work, achieving very high specific energy (Watts per m2). This results in highly localized heating and a very small HAZ. The energy from the laser beam rapidly heats the material over a very controlled and limited area, causing it to melt. Then the two (or more) parts fuse together in the cooling melt pool. The heat source in laser welding is localized, allowing for precise control over the process and minimal heat input into the surrounding area.
In MIG welding, the heat source is a direct current electric arc that is established between the workpiece and a consumable filler wire that is a sacrificial and joint-deposited electrode. The filler wire is continuously fed through a welding gun, and when the wire contacts the workpiece, an arc is established. The plasma that results from this arc heats the workpieces.
The intense heat of the plasma melts both the filler wire and the joint area of the metal, creating a weld pool. The heat in MIG welding is distributed over a larger area and with considerably less finesse and control than in laser welding. As a result, the arc length, size of the weld pool, and the HAZ are typically larger than in laser welding.
What Are the Equipment Requirements for Laser Welding Compared to MIG Welding?
The equipment requirements for laser welding and MIG welding differ significantly due to the different welding processes involved. The equipment for laser welding includes:
- Laser source
- Optics and beam delivery
- Automation
- Control system
The equipment for MIG welding includes:
- Power source
- Wire feed
- Welding torch
- Gas supply
- Control system
- Wire and consumables
It's important to note that the specific equipment requirements may vary depending on the application, materials, and desired weld quality. The complexity and cost of the equipment can also vary between different models and manufacturers.
Which Welding Process Offers Better Control Over the Welding Process
Laser welding generally offers better control over the welding process compared to MIG because of the following factors such as: greater precision in heat input, ability to complete narrow and deep welds, minimized HAZ, precision, and minimization in bead formation, and the relative ease in automation and roboticization.
MIG welding offers control over welding parameters such as voltage, wire feed speed, and gas flow rate; it is less precise and controlled than laser welding. In particular, it generates a larger heat-affected zone (HAZ) and wider weld bead. Continuous filler wire/electrode introduction drives much of the outcome in MIG welded joints.
Which Welding Process Is More Precise: Laser Welding or MIG Welding?
Laser welding is generally considered more precise than MIG. Laser welding enables finesse to control the heat introduced into the workpiece. Tightly focused and controlled heat imposes a concentrated and localized temperature rise. By this means, laser parameters such as pulse width modulation and source intensity can be used to apply very high specific energy at the small melt pool, making the process fast. Speed prevents excess conduction into the surrounding materials, reducing the HAZ and distortion risk.
This produces narrow welds that can have joint geometry that allows deep penetration, affording a high aspect ratio.
A joint design that provides deep shoulders and a closely joined well can allow welds that collapse those shoulders from the bottom upwards, forming a melt/fusion zone the depth of the shoulders and barely wider than the gap between them.
The process enables precise control over the weld bead shape and size, using the material from joint shoulders that can be placed with precision into a systematic and regular melt pool. This level of control enhances weld integrity and aesthetics, equipping designers to feature, rather than minimize, welds.
How Does the Weld Quality Differ Between Laser Welding and MIG Welding?
The weld quality between laser and MIG welding differs in several regards. In laser welding, greater aptitude in regulating heat input allows for greater finesse in bead formation and penetration. Narrow and deep welds can result from intelligent joint design, providing a deep well and intrinsic filler material in the pre-welded structure. The minimized HAZ prevents ugly welds and distortion of collateral areas. Precision and minimization can allow automated or skilled, manual bead formation to be aesthetically pleasing and proportionate to the joint.
In MIG welding, the weld beads tend to be large, due to the broader heat distribution. Heat input is also larger, and more distortion results.
Is Laser Welding Faster or Slower Than MIG Welding, Especially for Thin Materials?
Laser welding is generally faster than MIG, particularly for thinner materials. The high specific energy of laser welding results in a smaller melt pool that can form more quickly. It also allows the leading edge of the melt pool to propagate quickly, enabling fast joint processing. The absence of physical contact enables uninterrupted and continuous welding, improving processing speed. Additionally, automation allows greater consistency and removes hesitant processing in more difficult areas.
Can Laser Welding and MIG Welding Be Used Together?
Yes, laser welding and MIG welding can be used together in some contexts. The combination of these two welding processes is known as hybrid welding or laser-MIG welding. Hybrid welding offers advantages in mixed material assemblies with large variations in the weld or parts scale and cosmetic needs. MIG cannot handle mixed materials or very small welds on delicate parts, but it does enable rapid welding of simpler, heavier parts of common or closely related materials.
Summary
This article presented laser welding vs. MIG welding, explained each of them, and discussed the basics and their differences. To learn more about laser welding and MIG welding, contact a Xometry representative.
Xometry provides a wide range of manufacturing capabilities, including sheet cutting and other value-added services for all of your prototyping and production needs. Visit our website to learn more or to request a free, no-obligation quote.
Disclaimer
The content appearing on this webpage is for informational purposes only. Xometry makes no representation or warranty of any kind, be it expressed or implied, as to the accuracy, completeness, or validity of the information. Any performance parameters, geometric tolerances, specific design features, quality and types of materials, or processes should not be inferred to represent what will be delivered by third-party suppliers or manufacturers through Xometry’s network. Buyers seeking quotes for parts are responsible for defining the specific requirements for those parts. Please refer to our terms and conditions for more information.
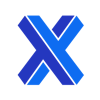