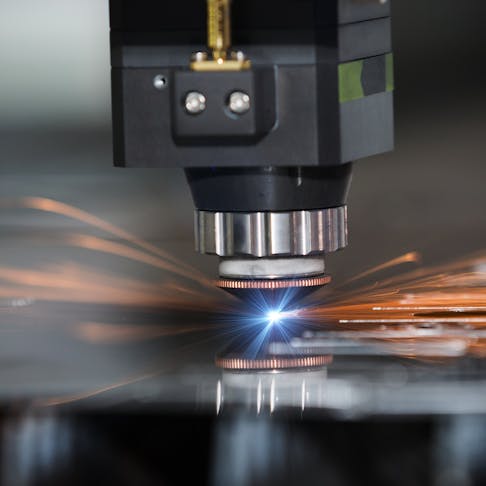
6 Applications of Laser Welding in Industries
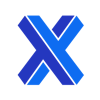
Laser welding is an advanced fabrication process that is used in industries including automotive, medical, aerospace, electronics, jewelry, and tool and die manufacturing. The laser welding process uses an intense laser to apply heat to the seam which fuses the two materials. Laser welding’s main advantage over traditional techniques is that it is cooler, resulting in fewer internal stresses in the joint. This process achieves a strong bond in applications in which the weld only penetrates less than 1 mm deep.
1. Automotive Industry
The automotive industry encompasses a wide range of organizations and activities related to the manufacturing of motor vehicles, including but not limited to design, development, manufacturing, production, and maintenance. The role of laser welding within the automotive industry has significantly increased over the past few years, largely due to production efficiency, quality, and cost-effectiveness. Automotive components such as: solenoids, engine parts, air conditioning units, alternators, fuel injectors, and filters are just some examples of the types of parts that lasers help produce. Several different types of laser welding are currently used for automotive applications such as: blue direct diode, fiber, pulsed disk lasers, pulsed neodymium-doped yttrium aluminum for smaller parts, spot, and seam welds. There has been a growing trend of fiber lasers being employed within the automotive industry recently.
2. Medical Industry
The medical industry provides healthcare treatment, medical equipment, and drugs for the general public. For many medical applications such as implants, very thin metal is used, and a precise weld is required, making laser welding a desirable option. Laser welding works by focusing a high-power laser into the seam between materials to melt and fuse the parts. The medical industry frequently uses micro welding, in which welds reach a depth of less than 1 mm. To carry out this form of welding the medical industry often uses Nd:YAG and Continuous Wave (CW) lasers. The benefit of this type of welding is that very accurate welds can be made on products including pacemakers, surgical blades, and endoscopic equipment.
3. Aerospace Industry
The aerospace industry uses laser welding for its precision in many applications—from security metal detectors to airframes. The aerospace industry requires very high-quality welds as they will be exposed to long working life and experience lots of stress. Aerospace laser welding is unique as it uses a filler wire to create stronger welds. This is necessary due to the requirement for aerospace structures to be highly resilient to fatigue. For this welding, the industry uses fiber lasers. Laser welding benefits the aerospace industry by reducing the total number of rivets used and (therefore) aircraft weight. This is important as aircraft manufacturers are always seeking ways to reduce an aircraft's weight—even by grams. The aerospace industry takes time to adopt new processes due to the need for extensive qualification; however, one application in which laser welding is commonly used is in the fabrication of fuel tanks.
4. Electronics Industry
The electronics industry produces products for an extensive range of applications and purposes. However, the most advanced electronic equipment is becoming increasingly intricate. The distance between pins can be as small as 0.3 mm, which is too close to prevent bridging with traditional welding methods. The electronics industry uses a standard laser welding process and employs Nd:YAG, continuous wave, fiber, and pulse laser welders. The benefit of using laser welding techniques is the ability to produce precision welds for small, advanced electrical components. Examples of laser welding in the electronics industry would be in the manufacture of control units and certain types of transistors.
5. Jewelry Industry
The jewelry industry produces wearable consumer goods which range in quality and often incorporate precious stones, rare metals, and intricate designs. The jewelry industry uses laser welding to accurately produce and repair products that are intricate and delicate by design.
The industry uses a “free moving” concept in which the laser beam is stationary and the operator can safely use their hands to move the jewelry in front of the beam for welding. The benefit of using a “free moving” laser welder is that it is safe to operate and relatively easy to use. Laser welding machinery can be used to create most forms of jewelry, for example, rings and bracelets.
6. Tool and Die Industry
The tool and die industry is a highly skilled industry specializing in manufacturing parts for machines, equipment, and other products such as: jigs, fixtures, dies, plastic molds, and cutting tools. Laser welding is capable of extending the life of mold tools, which is a critical design feature for these components. Laser welders also operate at a lower heat than conventional welding, eliminating the need for preheating a repair and reducing the internal stresses created by the heat of other welding processes. Pulse laser welding systems are the most efficient form of lasers due to the direct heat focus and precision that avoids the damaged surfaces often associated with conventional welding systems. The construction of precision tools that are used to cut, shape, and form metal in the tool and die industry is an example of the implementation of laser welding within this industry.
How Efficient and High-Quality Is Laser Welding Compared to Traditional Welding Methods?
In comparison to traditional welding methods, laser welding is much more efficient and the output is of a much higher quality. Laser welding functions as a beam of light that provides a concentrated heat source to melt materials, which then fuse upon cooling. Therefore, the application of laser welding requires less heat than conventional welding methods as the heat-affected zone (HAZ) is much smaller and more concentrated. As there is less heat required, this also translates to a lower risk of distortions and deflections in the final output, making it much higher quality. The processing speed of laser welding is much greater than traditional welding methods, making it far more efficient. For more information, see our guide on What is Laser Welding?
Can Laser Welding Be Used To Weld Dissimilar Metals?
Yes, laser welding can be used to weld dissimilar metals such as: brass-copper, copper-nickel, low-carbon steel-copper, nickel-titanium, titanium-aluminum, copper-titanium, and titanium-molybdenum. It can be challenging to form a true metallurgical bond at the weld seam for dissimilar metals, however, this can be overcome by creating a mechanical “entanglement.” This is a combination of dissimilar metals to ensure they are physically held together with enough mechanical strength to ensure a connection and can be achieved by physically pressing together the two metals and using a series of laser pulses to forge them both together locally.
Can Laser Welding Be Used To Weld Non-Metallic Materials?
Yes, laser welding can be used to weld composite materials, glass, and in some cases, ceramics. Welding ceramics can be more complex—the materials must not crack under the high temperature of the laser beam. To mitigate this, preheating is necessary to roughly 1,500 degrees Celsius and must be performed in the air.
What Are the Advantages of the Application of Laser Welding?
The accuracy and precision of the laser welding machine is the most significant advantage of its application. The depth and speed of welds created by the laser’s extremely powerful and focused beam of light enable a high volume of production that is extremely efficient. The restricted heat, minimal distortion, and precision with which lasers can join multiple pieces of metal together make it a highly desirable and effective method of manufacturing. Laser welding can operate at room temperature, or take place under special conditions such as within a vacuum or some gas environments. Finally, it can be safer for workers than other methods of welding in circumstances when the laser beam can be operated from a distance.
What Are the Disadvantages of the Application of Laser Welding?
Laser welding requires highly skilled operators to use the machine due to the high precision with which the laser beam works. Once the laser is focused, the spot size is incredibly small and the weld is narrow, therefore initial beam positioning is crucial to ensure accuracy. Handlers of the laser welding machine must therefore be highly trained. Another disadvantage is the expensive initial capital investment in acquiring the machine. Furthermore, there is a high cost of training the operators to a level at which they can safely and correctly use the laser welding machine. One final disadvantage of the application of laser welding is the potential health risks associated with it. The intense heat and light generated by the lasers pose a risk of burns and damage to eyesight if adequate precautions are not taken, and the fumes produced can be harmful if inhaled. For more information, see our guide on the Disadvantages of Laser Welding.
What Are Some Challenges in the Application of Laser Welding in the Manufacturing Industry?
The laser welding machine produces the beam for the welding process and requires a high-voltage power supply to operate. Shielding gas can sometimes be used to prevent any contamination from being released into the atmosphere. One of the challenges with laser welding machinery is the high capital and maintenance costs. On the other hand, this challenge can be balanced out by the decreased post-weld processing costs—as laser welds are so clean, they require no subsequent grinding. Another challenge is that the energy conversion efficiency is much lower than expected, roughly 10%. Additionally, whilst the precision of the laser beam is an advantage to many forms of manufacturing, it can be challenging to maintain 100% accuracy at all times, meaning there is a low gap tolerance. If the end product doesn’t meet the high-precision threshold expected of laser welding, this can lead to waste. However, this can be mitigated by ensuring operators have undergone the correct training and have the right skill set to manage the laser welding machine.
What Is the Difference Between Laser Welding and TIG Welding?
Laser welding has a much lower contamination risk than TIG welding and is therefore much more commonly used in the manufacturing of equipment such as medical instruments. The higher precision of a laser beam makes it much more accurate to create smaller and finer detailed apparatus. Laser welding enables the bonding of much thinner materials and greater tensile and bending strength. Unlike laser welding, arc welding requires filler or bonding material to join two pieces of metal. Laser welding simply creates a direct bond between metals, leaving no excess filler behind.
Summary
This article presented laser welding applications, explained them, and discussed the various industries in which laser welding is used. To learn more about laser welding, contact a Xometry representative.
Xometry provides a wide range of manufacturing capabilities, including sheet cutting and other value-added services for all of your prototyping and production needs. Visit our website to learn more or to request a free, no-obligation quote.
Disclaimer
The content appearing on this webpage is for informational purposes only. Xometry makes no representation or warranty of any kind, be it expressed or implied, as to the accuracy, completeness, or validity of the information. Any performance parameters, geometric tolerances, specific design features, quality and types of materials, or processes should not be inferred to represent what will be delivered by third-party suppliers or manufacturers through Xometry’s network. Buyers seeking quotes for parts are responsible for defining the specific requirements for those parts. Please refer to our terms and conditions for more information.
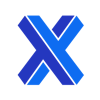