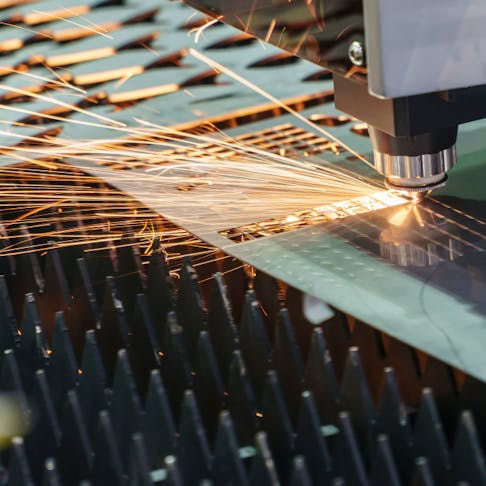
Laser Cutting Cost Calculator: Significance, Factors Affect Cost, and Benefits
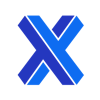
Precision manufacturing requires accurate cost estimation and budget planning for efficient resource allocation and optimization. Laser cutting calculators play a vital role in this process, providing valuable insights and benefits for precision cutting projects. Manufacturers can make informed decisions, streamline their operations, and maximize profitability by utilizing a laser cutting calculator.
Laser Cutting Calculator
The Significance of a Laser Cutting Cost Calculator
Laser cutting calculators are invaluable tools in the field of precision manufacturing. They assist manufacturers in accurately estimating the costs associated with laser cutting projects. By leveraging these calculators, manufacturers gain a deeper understanding of the cost components involved, allowing them to plan their budgets effectively and make informed decisions regarding resource allocation.
The primary benefit of laser cutting calculators is their ability to optimize costs. Manufacturers can identify areas where cost reductions can be achieved by accurately estimating the expenses associated with laser cutting. This includes evaluating different material options, optimizing design complexity, adjusting cutting speed, selecting the appropriate machine power, and optimizing production quantity.
Factors Affecting Laser Cutting Costs
Several factors influence laser cutting costs. Understanding these factors is crucial for optimizing costs and maximizing efficiency in precision cutting projects. Here are some key considerations:
Material Selection
The choice of material has a significant impact on laser cutting costs. Different materials have varying costs and cutting characteristics. Manufacturers need to consider factors such as material type, thickness, and availability when selecting the most suitable material for their project. Optimal material selection can lead to substantial cost savings.
Design Complexity
The complexity of the design plays a crucial role in determining laser cutting costs. Designs with intricate features, tight tolerances, and complex geometries require more time and effort to cut accurately. Simplifying designs without compromising functionality can reduce machining complexity and lower costs.
Cutting Speed
Cutting speed directly affects laser cutting costs. Faster cutting speeds result in higher productivity but may require more power. On the other hand, slower cutting speeds can be more precise but may lead to longer production times. Finding the right balance between cutting speed and cost is essential for optimizing efficiency and maintaining quality.
Machine Power
The power and capabilities of the laser cutting machine can impact costs. A Laser machine with higher power can handle thicker materials or more intricate cuts more efficiently but may come at a higher cost. Assessing the project's specific requirements and selecting an appropriate machine power level is crucial for cost optimization.
Production Quantity
Production quantity influences laser cutting costs through economies of scale. Larger production runs often offer cost advantages per part compared to smaller quantities. Analyzing batch sizes and considering the cost per part can help optimize production quantity and reduce overall costs.
How Laser Cutting Calculators Work
Laser cutting calculators employ sophisticated algorithms and formulas to estimate cutting costs accurately. They require specific inputs to generate reliable outputs. Here are some key inputs and outputs considered by laser cutting calculators:
Material Type
Laser cutting calculators consider the choice of material as a crucial input for cost calculation. Different materials like metals, plastics, and composites have varying costs and cutting characteristics. Accurate material selection ensures precise cost estimation.
Material Thickness
The thickness of the material significantly impacts laser cutting costs. Thicker materials may require more laser power or multiple passes, affecting overall cost. Laser cutting calculators consider material thickness an essential input for accurate cost estimation.
Quantity
The quantity of parts or components to be cut directly influences the cost calculation. Laser cutting calculators factor in economies of scale to determine cost advantages based on batch size. Accurate quantity input allows for precise cost estimation.
Cutting Parameters
Cutting parameters, including cutting speed, power, focal length, and assist gas selection, influence laser cutting costs. These parameters directly affect the efficiency and quality of the cutting process. Laser cutting calculators consider these parameters to provide accurate cost estimates.
Machine Utilization
Laser cutting calculators consider machine utilization factors such as availability, setup time, and efficiency. These factors impact the overall cost estimation by considering the effective use of the machine and minimizing idle time.
Benefits of Using a Laser Cutting Calculator
Utilizing a laser cutting calculator offers several benefits for manufacturers in the precision cutting industry:
Cost Optimization
Laser cutting calculators enable cost optimization by providing accurate cost estimates. Manufacturers can plan and allocate resources efficiently, ensuring that projects stay within budget. By identifying cost-saving opportunities, manufacturers can optimize their operations and maximize profitability.
Budget Control
Laser cutting calculators assist in budget planning by providing accurate cost projections. Manufacturers can set realistic budgets based on reliable cost estimates, reducing the risk of overspending or underfunding projects.
Project Planning
Laser cutting calculators aid in project planning by providing detailed cost breakdowns. Manufacturers can assess the feasibility and profitability of different projects before committing resources, enabling them to make informed decisions.
Material Efficiency
Laser cutting calculators help optimize material usage by considering material type, thickness, and quantity. Manufacturers can reduce costs and improve sustainability by minimizing material waste and maximizing material efficiency.
Summary
This article presented laser cutting calculators, explained them, and discussed the factors that affect costs for projects. To learn more about laser cutting, contact a Xometry representative.
Xometry provides a wide range of manufacturing capabilities, including sheet cutting and other value-added services for all of your prototyping and production needs. Visit our website to learn more or to request a free, no-obligation quote.
Disclaimer
The content appearing on this webpage is for informational purposes only. Xometry makes no representation or warranty of any kind, be it expressed or implied, as to the accuracy, completeness, or validity of the information. Any performance parameters, geometric tolerances, specific design features, quality and types of materials, or processes should not be inferred to represent what will be delivered by third-party suppliers or manufacturers through Xometry’s network. Buyers seeking quotes for parts are responsible for defining the specific requirements for those parts. Please refer to our terms and conditions for more information.
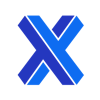