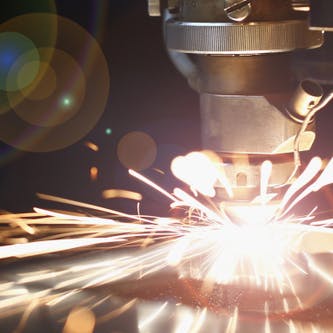
8 Steps of Laser Cutter Process (Laser Cutting)
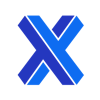
Laser cutting is an important industrial process that is rapidly becoming the primary method for cutting materials. It offers faster and cleaner results with less labor and overhead costs than most other approaches. A laser cutter uses a coherent light source to produce a collimated beam of light energy. It is then focused on a small spot on the surface of the material to be cut.
Given the proper type of laser, nearly all material types can be cut this way. Sheets of hardened steel and complex composites 100 mm thick pose no challenge when the equipment and operation are optimized.
Listed below are the 8 steps of the laser cutting process:
1. Material Preparation
Workpieces must be properly prepped in order to ensure a precise cut. Laser cutting can be performed on a wide spectrum of materials, including metals, plastics, composites, glass, rock, fabrics, and more. However, lasers create hazards when applied to certain materials, and other items may not respond well (or at all) to laser cutters. For example, PVC produces highly toxic chlorine gas when burned, and ABS (acrylonitrile butadiene styrene) simply pools and bubbles rather than cutting. Additionally, laser systems can only cut materials up to a certain thickness limit. The limit depends upon the absolute laser power, the beam quality, and the absorption spectrum of the material.
To prep the laser cutter, first securely position the workpiece on the laser cutting bed. Load the design into the cutter’s computer system. Validate that the file is composed of single lines, without color or layer issues that might interfere with the cutter software. Check that the laser cutting parameters such as laser power, speed, focal length, gas assist, etc. are suitable for your project and material. Ensure that your machine’s extraction and filtration systems are functioning and that the workspace has adequate ventilation.
2. Laser Beam Generation
Laser light is generated through a process called stimulated emission (LASER means Light Amplification by Stimulated Emission of Radiation). It begins with a laser medium — a solid, liquid, or gas (unique or blended) whose atomic structure can be excited to higher energy levels. The medium is pumped with energy to generate these higher energy states. This can be done through electrical discharge, optical (flash tube, another laser, etc.) pumping, direct electrical stimulus at a semiconductor junction, or chemical reactions that generate flashes of energy emission.
When a photon of the correct energy interacts with an atom in this excited state, it stimulates the emission of an additional photon. The atom briefly enters a higher energy state that cannot be sustained. This stimulated emission process creates two photons that are identical in terms of their energy, phase, direction, and polarization. The newly emitted photon is in phase with and moves in the same direction as the incident photon, which leads to the amplification of light. A chain reaction of these photomultiplication reactions generates a stream of coherent photons within a narrow frequency range.
These generated photons are reflected between mirrors placed at either end of the laser medium. This creates an optical cavity or resonator which allows the photons to build up in intensity through multiple passes. However, one of the mirrors is partially transparent, allowing a predictable proportion of the light to exit the resonator as a coherent beam.
3. Beam Focusing
The process of focusing a laser requires the manipulation of the laser beam to draw its energy into a smaller area. This is typically done with lenses or mirrors and improves the specific energy, power density, and precision in applications such as: cutting, drilling, welding, or laser microscopy. A smaller focal spot results in a narrower cut and a longer focal length creates a more uniform kerf.
There are various ways to focus the beam, depending on the laser system’s characteristics. A convex lens or converging lens is the most common solution. Diffraction within the lens bends the light rays, causing them to converge at a ‘focal point’ a specific distance from the lens surface. The distance between the lens and the focal point determines the degree of beam convergence or divergence. The beam’s quality, meanwhile, defines how small that spot can be, and becomes the limiting factor of the laser’s specific energy at the ‘work’ point.
Mirrors can also be used to focus beams, functioning in much the same way as those in a reflecting telescope. Concave mirrors are designed to make reflected light converge at a single point. Mirrors can be used alone or in combination with lenses for energy concentration.
In higher-end systems, particularly those requiring extreme precision, adaptive optics enhance beam control in real time. These systems use digitally controlled, deformable mirrors or variable-focal-length lens systems to correct for distortions and aberrations in the beam caused by imperfections in the optics or transient obstructions. Since they actively monitor and adjust the focal length, the beam can be focused and maintained at optimum quality.
4. Cutting Parameters Setup
The machine’s laser cutting parameters need to be optimized in order to get the best possible quality out of the cut. The laser energy level is the main driver in determining the beam’s intensity, which, in turn, affects cutting speed and depth. Higher power settings allow for faster cutting but may result in a larger HAZ (heat-affected zone) if not properly tuned. HAZ size is directly related to beam power, beam conditioning, and the response of the target to the incident energy. Speed significantly affects the quality of the cut and the process’s productivity. Higher cutting speeds generally produce smaller heat-affected zones, as there is less time for heat to spread out from the laser’s point of incidence. However, high speeds may also mean that melt residues don’t clear the cut but instead bubble into a rough, imperfect cut.
Adjust the focal point of the laser beam to a position at the material surface or slightly below it. This increases the specific energy (power per unit area) at the critical cut initiation point by minimizing the spot size. In some cases, you may want to set the focus below the upper surface of the target to control the form of the kerf or cut zone.
Select the diameter of the gas assist nozzle based on the material thickness and desired cutting quality. Smaller nozzle diameters provide finer cuts while larger nozzles may allow faster cutting speeds and better clearance.
It takes time to pierce through any item and thicker materials take longer. The exact values depend heavily on the material thickness, type, and laser power and should be determined by a test.
The kerf width refers to the width of the cut made by the laser. It is influenced by several factors, including laser power, cutting speed, focal quality, and material properties. The kerf width must be carefully considered when manufacturing parts with tight tolerances.
In some cases, the material benefits from preheating or post-heating. Preheating improves the cutting process because the laser doesn’t have to do as much work to get all the way through thick workpieces. Post-heating reduces residual stresses in the cut areas which might distort the part.
Differences in materials will demand that you adjust the cutting parameters. Reflectivity, thermal conductivity, and melting point influence the machine’s ability to start or continue a cut. Consult material-specific guidelines and perform test cuts to determine optimal settings.
Start out with the manufacturer's guidelines for the specific laser system and material being cut. Test cuts will show you which adjustments to make to your parameters. You’ll likely need multiple test iterations in order to fine-tune your setup for complex projects.
5. Cutting Process
Once the machine parameters are validated by testing, the cutting process can begin. The laser cutting machine will follow its programmed instructions. The beam rapidly heats and vaporizes the material. The gas assist blows vapor and droplets clear and cools the post-cut areas, creating a narrow kerf along the desired cutting path.
For larger cutting jobs or when cutting multiple parts, the laser cutting machine will operate continuously unless forced to pause to reposition the workpiece or clean the nozzle. More capable equipment may ‘observe’ other reasons for stoppages or operator intervention.
After the cutting is complete, the cut parts will often need to undergo additional post-processing steps such as cleaning, deburring, or surface treatment before the product can be called complete.
6. Motion Control
Programmed movement is achieved either by moving the cutting table or the optics head (or occasionally both). Larger machines typically have mobile optics because the optical head has far less mass than a large workpiece, allowing for faster maneuvers. Move time between cuts can suck up significant process time, especially when large plates and heavy loads must be positioned. Smaller industrial machines with lower cutting capacities will commonly move the cutting platform along at least one axis of motion because it simplifies the optical setup. Desktop machines, meanwhile, commonly feature fixed lasers, so all motion is made by the cutting table.
In all cases, the motion is controlled using a G-code-based CNC approach. Motion is driven by stepper motors in smaller machines and often by closed-loop controlled DC motors on larger machines. These positioning motors get movement instructions from the G-code which the computer controller converts into motor drive and positioning instructions.
7. Gas Assist (Optional)
Gas assist serves a range of purposes in laser cutting. Melt material and ash removal is usually the most critical function of gas assistance. Natural materials generally char at the cut point and the remains are blown away. Metals may partially vaporize but most of the residue in the kerf is molten material that needs to be cleared, exposing further depth in the cut zone. The fast-moving gas also serves to cool the surrounding uncut material and minimize the HAZ.
Many materials release smoke and vaporized material when cut. This can deposit residues onto the surrounding material or onto the optics, either reducing the product’s surface quality or disrupting beam intensity and quality. Gas assist helps to keep the whole cut area and optics clear of these effects.
In some cases, the gas assist can enhance the cut process more directly by introducing oxygen into the cut. Some of the material can be oxidized and/or literally burnt away. This is particularly valuable when cutting thick steel items.
8. Collection and Finishing
Cut parts will remain in place on the cutting table at the end of cutting operations. They can be safely removed once the laser is turned off and the machine has ceased movements. Take care, though, because cut parts can have sharp edges and hot residue.
Laser cutting is a very high-temperature process, so give the parts sufficient cooldown time before handling them. You also may need to make special handling considerations to prevent damage; many items can get scratched if they’re stacked without interleaf protection.
Important finishing processes may include: deburring, stress relief operations, chemical or mechanical surface cleaning, etching, plating, painting, and careful packaging to maintain the finish.
What Is a Laser Cutter?
A laser cutting machine generates a high-energy laser beam that is then directed to the optical cutting head via light pipes or mirrors. The cutting head optics focus the coherent energy on a small spot. That heats the target material until it melts, chars, or vaporizes. Any remaining char, smoke, or melted material is then blown clear of both the cut and the optics apparatus to allow the cut to penetrate deeper and progress along the cut path.
An X-Y transport mechanism moves either the workpiece, the optics head, or a combination of the two so that the laser traces out the preprogrammed cutting path until the finished part can be extracted from the sheet material. For more information, see our guide on How Do Laser Cutters Work.
When Were Laser Cutters First Used in Manufacturing?
Ruby-laser cutting machines were the first type to be successfully created by Western Electric in the mid-1960s. These devices worked at low power outputs and the earliest cutting applications involved drilling fine holes in diamond dies. Boeing was the first company to experiment with CO2 lasers to cut otherwise intractable materials. The first marketed laser cutting machines were developed by Western Electric, with sales beginning around 1975.
New laser types and improved cutting techniques have expanded the sector to the point where some laser cutters are small and cheap enough for home use and others serve in large-scale manufacturing.
How Does a Laser Cutter Work?
A laser cutting machine is a specialist CNC device with generally low operational overheads. The machine generates a high-energy beam of coherent light radiation with an integral resonant chamber. A collimator tunes the beam to ensure its divergence is minimized. It directs the beam, either via mirrors or light pipes to a focus apparatus. Then optics/lenses focus the beam on a small spot to concentrate the energy and initiate a cut. The energy melts and/or vaporizes material along the programmed cut line. In some cases, it needs more than one pass to cut through the workpiece’s entire thickness. Air assist blows char, smoke, and melted material from the cut to clear it and cool the surroundings. A CNC axis system moves either the laser optics, workpiece, or both in the necessary motions to complete the cut process. This is usually done in only two dimensions (the X-Y plane), but some machines create contoured surfaces by adding Z-axis motion. In some cases the motion can have additional axes, to allow closer conformance to rounded pipes or even more complex 3D objects. For more information, see our guide on the Use of Laser Cutting.
What Types of Materials Can Used for Laser Cutters?
Certain materials require specific laser types (e.g., CO2, fiber, or solid-state lasers) and adjustments to the power, speed, and type of assist gas.
Laser cutting is applicable to most metals and plastics, wood, fabrics, composite materials, glass, and ceramics, including:
- Carbon steel, stainless steel, and mild steel
- Aluminum
- Brass, bronze, and copper
- Titanium
- Acrylic (PMMA)
- Polycarbonate (PC)
- Polypropylene (PP) and polyethylene (PE)
- Cotton
- Polyester
- Felt
- Silk
- Leather
- Carbon fiber-reinforced polymers (CFRP)
- Fiberglass-reinforced plastics (FRP)
What Are the Advantages of Laser Cutters in Manufacturing?
Laser cutting offers advantages over many other manufacturing processes. Some of the advantages include:
- The machine’s exceptional precision and repeatability keep even intricate and complex cuts consistent and within tight tolerance parameters throughout long production runs.
- The process is versatile enough to cover a wide range of materials including metals, plastics, woods, fabrics, and more. It can accommodate both thick and thin examples of those materials.
- It is a non-contact process, so no aspect of the cutting imposes any significant external forces on the material being cut. This limits the need for custom tooling, minimizes or prevents material deformation, and enables you to cut delicate or fragile materials with less risk.
- Laser cutting minimizes material waste. The narrow laser beam creates a small kerf, so very little material is lost. Not only can most of the material be put to use, but you can also design nested parts with minimal clearances between them.
- It is a rapid cutting process that enables high-speed production of complex shapes in a single, rapid pass. The automation capabilities of laser cutting machines allow for continuous and uninterrupted operation, greatly increasing productivity.
- Laser cutters are flexible, allowing for cost-effective customization and on-demand production of single parts. Design changes can be rapidly incorporated into the G-code, enabling manufacturers to quickly respond to customer demands.
- The process eliminates the need for physical dies, molds, or cutting tools.
- The laser generates a small HAZ compared to other thermal cutting methods. The rapidity of the process prevents heat buildup and thermal distortion, minimizing the risk of damage to the part through processing.
- These systems incorporate safety features to protect operators and ensure a safe working environment including: fume extraction, fire suppression, and user interlocks.
What Are the Disadvantages of Laser Cutters in Manufacturing?
Although laser cutting offers many advantages over more traditional methods, there are issues to consider and barriers to some manufacturing applications. Some disadvantages include:
- Laser cutters — especially for high-powered systems with advanced features — can be expensive. Additionally, regular and highly skilled maintenance is required to keep the equipment in optimal working condition.
- Material thickness is a natural limit to the process. Some cuts may require multiple passes, reducing the procedure’s efficiency and speed.
- Highly reflective materials, including certain metals and plastics, can be challenging to cut using ‘typical’ setups because they reflect laser light or conduct heat differently than most. Some materials also emit hazardous fumes when laser cut, requiring additional safety measures. And some materials are simply not suited to laser cutting because of their thermal sensitivity or response to heating.
- Despite the minimal HAZ compared to other thermal cutting methods, laser cutting still introduces heat into the surrounding material which can adversely affect properties.
- When cutting thick or particularly resilient materials, the cutting speed may need to be slowed, requiring more power and slower feed rates to ensure effective cutting.
- While laser cutting is cost-effective for 2D cutting, it becomes more challenging and costly when cutting 3D shapes. Additional axes of laser freedom drive machine costs up significantly.
- High-energy lasers pose obvious safety risks that go beyond those of most hot processes. Adequate safety precautions must be followed to ensure operator safety.
How Much Does a Laser Cutting Machine Cost?
Low-powered home/hobby machines start at a few hundred dollars. Despite their limitations, such machines are widely and effectively used in many applications. Large industrial machines with laser powers in the tens of kilowatts can cost up to $1,000,000 and require special facilities and support equipment that add to this cost.
Do Laser Cutters Have Different Laser Powers?
Yes, laser cutters can run at different laser power settings. They are designed for a wide range of tasks. Paper- and card-cutting lasers may need less than 10W while large industrial machines are available with 10+ kW lasers.
Are Laser Cutters Able To Cut Stainless Steel?
Yes, with the correct setup, parameters, and power, many laser cutters can handle various thicknesses of stainless steel. For more information, see our guide on Lasers For Cutting Stainless Steel.
Can Laser Cutter Engrave?
Yes, some laser cutters can also do engraving. The difference between laser cutting and laser engraving is only how deep a cut is made. Laser engraving demands more precise power and throughput control than laser cutting. For more information, check out our guide on What is Laser Engraving.
Summary
This article presented the laser cutting process, explained each step, and discussed them in detail. To learn more about laser cutting, contact a Xometry representative.
Xometry provides a wide range of manufacturing capabilities, including sheet cutting and other value-added services for all of your prototyping and production needs. Visit our website to learn more or to request a free, no-obligation quote.
Disclaimer
The content appearing on this webpage is for informational purposes only. Xometry makes no representation or warranty of any kind, be it expressed or implied, as to the accuracy, completeness, or validity of the information. Any performance parameters, geometric tolerances, specific design features, quality and types of materials, or processes should not be inferred to represent what will be delivered by third-party suppliers or manufacturers through Xometry’s network. Buyers seeking quotes for parts are responsible for defining the specific requirements for those parts. Please refer to our terms and conditions for more information.
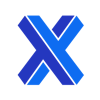