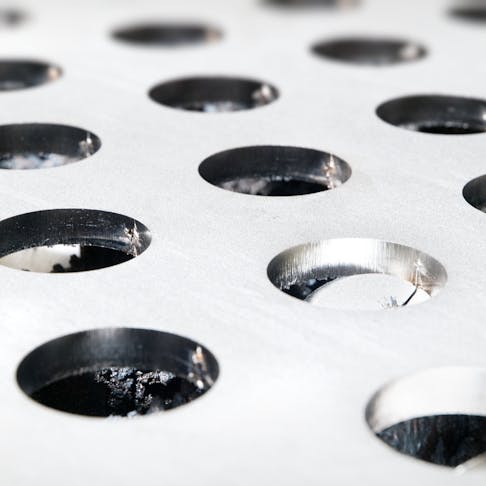
Laser Cutting Aluminum: Everything You Need To Know
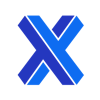
Laser cutting aluminum uses a tightly focused and collimated beam of light radiation to heat and melt/vaporize a small spot on the surface of the material. This melted material is then blown away with a gas stream, exposing deeper material which is similarly removed. By this means, a path is cut as the laser advances through the depth of the cut, and progresses along the line of the cut, to extract a CAD-designed component from a flat or formed sheet, an extruded section, or a tube, depending on the need.
This article will cover the nature of the techniques and process optimization to get the best results from laser cutting aluminum.
This article will discuss in detail the nature and process of laser cutting aluminum, its importance, and how it is optimized.
What Is Laser Cutting Aluminum?
Laser cutting aluminum is a manufacturing process that uses a high-powered and tightly focused laser beam. This is to precisely cut aluminum sheets or plates to exactly match CAD-specified shapes or patterns. It is a critically important method for metal fabrication, offering major advantages over more traditional cutting techniques. Laser cutting aluminum is common in various industries, including aerospace, automotive, electronics, signage, and architectural applications. It offers a precise and efficient method for cutting aluminum with high quality and consistency.
What Is the Importance of Laser Cutting Aluminum?
The laser cutting of aluminum holds significant importance in virtually all manufacturing sectors. It offers both versatility and cost-effectiveness. The laser cutting of aluminum can take place on flat and formed parts or a wide spectrum of thicknesses and alloys, with a single operation. The materials wastage of laser cutting is also very low. Additionally, laser cut parts produced by a good set-up and appropriate equipment require minimal or no post-processing to produce an acceptable finish on the cut faces. This ultimately removes the need for additional manufacturing stages.
How Does Laser Cutting Aluminum Work?
Laser cutting aluminum works by using a high-powered laser beam to melt and vaporize the material, creating a precise and clean cut. The applied beam is focused on a small spot, and its energy is transferred to the target material, heating it very rapidly. Thicker materials require the residual material that has not been vaporized to be then blown out of the active cut region with a gas or air assist.
How To Laser Cut Aluminum?
The specific details of the laser cutting process vary according to the type and power of the laser machine used and the specific operational parameters optimized by the operator. In general, the laser cutting process involves the following steps:
- Prepare the material by cleaning the surface and ensuring it is securely positioned on the cutting table.
- Set up the cutting parameters such as laser power, CNC-controlled feed speed and path, assist-gas type and pressure, and nozzle position. This involves trial and iteration of settings.
- Direct the focused laser beam onto the aluminum surface, rapidly heating and melting/vaporizing the material. Simultaneously, assist gas such as nitrogen is directed through a nozzle to blow away the molten metal and clear the kerf or cut path.
- The assist gas rapidly cools the newly cut region as the beam moves further along the cutting path.
How Effective Is Laser Cutting in Cutting Aluminum?
Laser cutting is strikingly effective in cutting aluminum, offering a variety of benefits over traditional cutting methods. These make the process the preferred solution for reliably extracting precision parts from both sheet and formed aluminum. For more information, see our guide on Aluminum Properties.
What Type of Laser Can Cut Aluminum?
Aluminum can be effectively cut by several types of devices, but the most commonly used for aluminum cutting are fiber and CO2 lasers. Both of these types offer specific advantages and are suitable for different applications and thickness ranges. Fiber lasers use optical fibers to both stimulate and deliver the laser beam to the cutting head. They are known for their high power density, excellent beam quality, and elevated energy efficiency. Fiber lasers are particularly effective for aluminum up to 25 mm in thickness. As such, fiber lasers represent key equipment in the precise and fast cutting of aluminum for applications in: automotive, aerospace, electronics, and signage usage, among others.
CO2 lasers use a mixture of carbon dioxide, nitrogen, and helium, excited by a laser or arc source as the stimulated emission medium. They are relatively economical to buy and suitable for a wide range of materials, including aluminum. This is despite the strong reflection characteristic of aluminum that coincides with the laser emission frequency. They are especially effective for thicker aluminum materials, typically above 6 mm (0.24 inches) as very high-power devices are relatively low-cost to buy.
For more information, see our guide on How Does a Fiber Laser Work.
Can Plasma Cutters Cut Aluminum?
Yes, plasma cutters can cut aluminum effectively and very fast. Plasma cutting is a versatile and widely used method for cutting various metals, including aluminum. Plasma cutting utilizes a high-velocity jet of ionized gas (plasma) to melt and remove the metal, creating a clean and precise cut. However, compared to laser cutting, plasma cutting may result in a wider heat-affected zone and considerably rougher (cut) edges. This does not prevent plasma cutting of aluminum from being a cost-effective solution in some sectors.
What Is the Role of Speed and Power in Laser Cutting Aluminum?
Speed and power are the defining parameters when laser cutting aluminum. Their impact on equipment cost, processing time, and finished part quality are critically important. The cutting speed directly affects the amount of heat input into the material. Slower cutting speeds allow time for more heat to be absorbed, potentially leading to a larger heat-affected zone and increased risk of material distortion. The intensity of the laser beam at the cut point is influenced by beam quality, collimation, focal equipment setup/quality, and the overall power of the laser. Higher power improves the cut depth and speed at which material can be processed. This directly drives the thickness capacity and productivity of the equipment.
Laser power affects the quality of the cut. Higher power levels allow for faster cutting speeds, but excessive power can also lead to a wider kerf width and potential material splattering. Additionally, aluminum is highly reflective, particularly at the emission frequency of CO2 lasers. To effectively cut aluminum when experiencing such reflection, laser systems require higher net energy levels to initiate melting. For more information, see our guide on Speed and Power.
What Is the Recommended Speed for Laser Cutting Aluminum?
The recommended cutting speed for laser cutting aluminum is highly variable and depends heavily on several factors. This includes: the thickness of the material, laser power, beam quality, and the specifics of the cutting system being used. For example, a thin aluminum sheet (up to 3 mm) benefits from higher cutting speeds, providing the laser power is sufficient to allow it. Cutting speeds in the range of 1,000–3,000 mm/min are widely reported.
Medium-thickness material (3–6 mm) needs cutting speeds that may range from 500–1,500 mm/min. Heavy-gauge aluminum plates (above 6 mm) need lower cutting speeds to achieve full penetration unless the available power is more than 10 kW. Faster cutting at these high powers and thicknesses prevents full penetration/clearance and can cause splattering. Cutting speeds in the range of 200–800 mm/min are commonly used for heavy aluminum plates.
How Much Is the Needed Power for Laser Cutting Aluminum?
The power threshold demanded for cutting aluminum relies on various factors, including: the thickness of the material, the desired cutting speed, and the specification of the cutter being utilized. The power needed can range from a few hundred watts to several kilowatts. For example, thin aluminum sheets (up to 3 mm or 0.12 inches) require a laser power of at least 500 W for 3 mm sheet and pro-rata for thinner material. Medium-weight aluminum (3 mm to 6 mm or 0.12 to 0.24 inches) needs power in the range of 1–3 kW for good results. Heavy-gauge plates (above 6 mm or 0.24 inches and up to 100 mm or 4 inches) need 3,000–8,000 watts or more, and higher power can be very beneficial in productivity/throughput terms. For more information, see our guide on Power for Laser Cutting.
What Is the Best Grade of Aluminum for Laser Cutting?
Various aluminum grades are processed by laser cutting, because of favorable characteristics. These grades of aluminum are: 6061, 5052, 5083, and 7075. These aluminum grades offer good weldability and excellent machinability. However, 7075 aluminum requires higher laser power levels and slower cutting speeds due to its high strength and hardness.
What Size of Aluminum Can Be Laser Cut?
Aluminum sheet that can be accommodated depends on the specific machine's bed size. Standard sheet sizes for aluminum, such as: 4 feet by 8 feet (1.2 meters by 2.4 meters) or 5 feet by 10 feet (1.5 meters by 3 meters). Most larger industrial machines are built to accommodate such stock, although some are larger still. Many machines used in large-scale production are set up to work with rolls of sheet, to allow a less disrupted process as the roll can be pulled through for a new cut batch. Desktop machines range in sheet capacities from a few inches diagonal, with approximately an A4-size sheet being widely accommodated.
Can a 10 mm Thickness of Aluminum Be Laser Cut?
Yes, a 10 mm sheet of aluminum is relatively easy to laser cut with good results, needing a power of 1–3 kW for high throughput.
What Are the Benefits of Laser Cutting Aluminum?
Laser cutting aluminum offers several benefits that make it a popular choice for various applications. These benefits are listed below:
- Delivers exceptional accuracy and precision.
- Can cut aluminum sheets up to the size of their bed or X-Y axis traverse distance, and process both flat and formed aluminum parts with ease.
- Fast and cost-effective, it enables high-speed cutting with minimal setup time and material waste.
- The highly localized heating and rapid cooling minimize the heat-affected zone. This reduces the risk of distortion and avoids degrading remaining material properties.
- Delivers clean, burr-free cuts, eliminating the need for post-processing.
- Highly amenable to being integrated into automated production lines, increasing productivity and reducing labor costs.
What Are the Challenges of Laser Cutting Aluminum?
While laser cutting aluminum offers numerous advantages, there are also challenges in the process. These are listed below:
- Aluminum is a highly reflective material, particularly in its polished state and particularly at the wavelength of key equipment such as CO2 lasers. This causes a proportion of the energy to scatter rather than be absorbed, reducing cutting effectiveness.
- The high thermal conductivity of aluminum results in rapid dissipation of heat which creates a limited heat-affected zone.
- The oxide layer (and anodizing) of aluminum can influence the cutting process, having different optical properties from the bulk metal.
- Laser cutting is suitable for a wide range of material thicknesses. However, cutting very heavy-gauge plates may require higher laser power levels and slower cutting speeds, because of the heat dissipation into the bulk.
- Material warping and distortion can be an issue, especially for thin and delicate aluminum parts.
- Can leave surface discoloration and oxidation in the heat-affected zone.
Is Laser Cutting Aluminum Expensive?
No, laser cutting aluminum is not expensive. While the equipment and operational setup deliver high throughput, aluminum laser cutting carries a high CAPEX burden. Profitability is achievable when there is sufficient work. In most applications, the processing cost is less than (often considerably less than) the raw material costs. The factors that contribute to the cost are: machine investment and maintenance costs, power, consumables, the complexity of the part, and set-up and programming.
Is Laser Cutting Aluminum Safe?
Yes, laser cutting is safe when the correct procedures are adhered to. All hot, high-power processes have associated risks and hazards that must be managed. For example, laser radiation is intrinsically dangerous when powers exceed a few watts. Laser cutting involves the use of intense radiation. Direct exposure is hazardous to the eyes and skin. Ensure laser safety measures are in place and fully implemented, including the use of protective eyewear, hazard signage, and proper enclosure or guarding of the laser cutting area. Laser cutting can generate sparks and molten metal spray. Fire prevention training of staff and systems must be in place, including fire extinguishers, fire-resistant work surfaces, and automated fire suppression systems.
Summary
This article presented laser cutting aluminum, explained what it is, and discussed its various applications. To learn more about laser cutting with aluminum, contact a Xometry representative.
Xometry provides a wide range of manufacturing capabilities, including sheet cutting and other value-added services for all of your prototyping and production needs. Visit our website to learn more or to request a free, no-obligation quote.
Disclaimer
The content appearing on this webpage is for informational purposes only. Xometry makes no representation or warranty of any kind, be it expressed or implied, as to the accuracy, completeness, or validity of the information. Any performance parameters, geometric tolerances, specific design features, quality and types of materials, or processes should not be inferred to represent what will be delivered by third-party suppliers or manufacturers through Xometry’s network. Buyers seeking quotes for parts are responsible for defining the specific requirements for those parts. Please refer to our terms and conditions for more information.
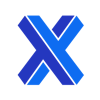