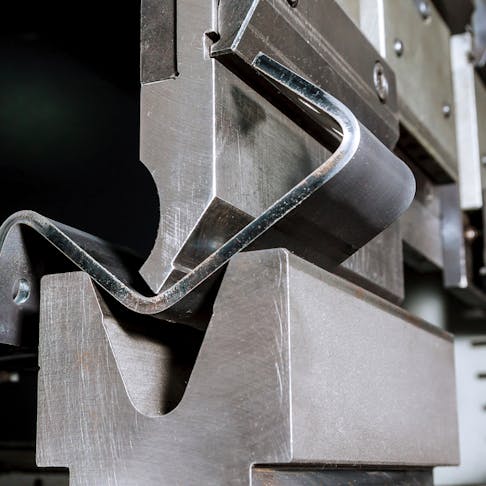
Sheet Metal Bending: Definition, Purpose, How It Works, Advantages, and Examples
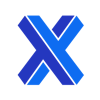
Sheet metal bending is the process of applying a force to a sheet of metal to produce a radius. The most common way to achieve this is a press brake. This process can be used in the manufacture of vehicle body panels, fridges, electronic casings, and brackets. Sheet metal bending is best suited for applications with lower production volumes or products using very thin metal for which casting is not effective.
What Is Sheet Metal Bending?
Sheet metal bending is the forming of metal into different geometries, by using a force to deform the metal. It is referred to as sheet metal bending as a thin sheet of metal is bent once, or multiple times, to form the final geometry. The thickness of sheet metal used can vary. The minimum thickness sheet metal can be bent is approximately 127 mm thick and the maximum will depend on the material type and thickness. Generally, sheet steel is no more than 6 mm thick. As a rule, the bend radius should be equal to or greater than the thickness of the material.
What Is Sheet Metal Bending Also Known As?
Sheet metal bending is also known as: forming, edging, folding, flanging, press braking, or die bending. The last of the names is used as some sheet metal bending is achieved using a die and punch system. Press braking refers to cases in which a press brake machine is used to bend the sheet metal.
What Is the Purpose of Sheet Metal Bending in Manufacturing?
The purpose of sheet metal bending is to form features onto a sheet of metal. This could be for creating body panels, reinforcement struts, floor panels, brackets, or doors. Sheet metal bending is a much faster, cheaper, and more efficient way of producing thin-walled parts, as opposed to machining them.
What Are the Industries That Use Sheet Metal Bending?
The use of sheet metal bending is widespread, including: in the construction, automotive, transport, aerospace, and infrastructure industries. Sheet metal bending can be used in every industry to create features such as: lips, joggles, flanges, and indents. Sometimes sheet metal bending is used to increase the stiffness of a sheet metal part.
How Does Sheet Metal Bending Work?
Sheet metal bending with a press brake works by aligning and holding the metal to be bent in the press brake tool. Once it is aligned, the press can move down and exert a force onto the metal, forming it into a new shape by producing angles. Press brakes can exert forces well in excess of 100 tons to bend steel upwards of 3 mm thick.
What Is the Step-by-Step Process of Sheet Metal Bending?
There are a few different machines that can be used to bend sheet metal. The most common is a press brake machine which itself can be mechanical and fully manual (usually used in small machine shops), or it can be computer numerically controlled (CNC) and uses a hydraulic system. The principles used in both machines are the same, but the way the operator interacts is different. This process below will focus on the operation of a CNC press brake machine:
1. Calculate the Design Parameters
Before using the press brake, calculate the design parameters including: force required, bend line (the point where the force is exerted), and the order of bends (if there are multiple). The die used to create the bends must also be decided.
2. Set Up the Press Brake
To set up the press brake, input the information calculated into the CNC machine, so it knows how much force to exert on the metal to create the right bend and in which order these bends will be carried out. The right tool and die must be attached to the press and brake, ready for bending.
3. Align the Part
Align the metal between the tool and die. When the machine is operated, it will bend the sheet of metal at the bend line.
4. Engage the Press Brake
Engage the press brake so that the force parameters—inputted into the CNC press brake at step 2—are applied. Once the press brake has bent the metal, the part can be removed and made ready for the next stage of production.
How Does Laser Cutting Improve Sheet Metal Bending Precision and Efficiency?
Laser cutting improves the efficiency of sheet metal bending by reducing the time needed to prepare the sheet metal for bending. Laser cutting also provides edges with tight tolerances. These edges can be used as data when using a press brake bending machine. A reduction in the precision of the cut edge would reduce the location accuracy of the bend. To learn more, see our guide on Laser Cutting Manufacturing.
How Does Fiber Laser Cutting Reduce Waste and Optimize Sheet Metal Bending?
Laser cutting can reduce waste and optimize sheet metal bending in two ways. Laser cutting reduces the number of errors made in cutting; this increases repeatability and reduces variability, resulting in the production of fewer scrap parts. Laser cutting also increases productivity by using an automated process to cut the metal. To learn more, see our guide on How Fiber Lasers Work.
What Are the Metals Used in Sheet Metal Bending?
There are a range of metals that can be used in sheet metal bending. Six metals are discussed below:
1. Steel
Steel is a very versatile metal that consists of iron and carbon. Steel is economical and has great strength and durability. There are a range of different steels that can be bent including mild steel and stainless steel. Mild steel is easily bent and used widely, including in a range of automotive applications.
2. Aluminum
Aluminum is a lightweight and cost-effective metal used in the aerospace, electronics, and automotive industries. Aluminum is easy to fabricate and benefits from a high strength-to-weight ratio and high corrosion resistance.
3. Copper
Copper is a soft metal that allows it to be easily bent and formed. It is also highly conductive, making it perfect for electrical applications. Copper is also naturally antimicrobial and recyclable.
4. Brass
Brass is an alloy consisting of zinc and copper. Brass is used a lot in sheet metal bending because of its aesthetic appeal and ease of fabrication. Because of its aesthetic appeal, it is used in decorative applications including: home hardware, architecture, and instruments. Brass benefits from high machinability, low friction, and corrosion resistance.
5. Stainless Steel
Stainless steel, like regular mild steel, is made of iron and carbon, but with the addition of chromium and nickel. Due to the extra chromium and nickel, stainless steel is also harder and work hardens as it bends. This means that stainless steel usually requires a press brake rather than bending by hand. Stainless steel, which uses chromium to protect against degradation, is used in medical and food processing equipment.
6. Galvanized Steel
Galvanized steel, like stainless steel, is highly corrosion-resistant. This is because galvanized steel has a zinc coating. In addition to having an improved service life, galvanized steel components are lower cost than other forms of corrosion-protected steel.
How Long Does It Take for Sheet Metal Bending To Finish?
The time taken to bend sheet metal is subjective to a number of factors. These factors include if the machine is already set up for the bend and the number of bends in that part. If the machine requires the changing of tooling to perform the bends, then it will add extra time for an operative to change the tooling. Additionally, the time taken will increase with the number of bends. If fully automated, with the machine prepared, bending can take a matter of seconds. If machine setup is required, bending may take up to an hour depending on the complexity of the setup.
How Accurate Is Sheet Metal Bending?
The final dimensions of a sheet metal part not only rely on the bending of the part but also on the size. If the sheet is cut accurately, it can be bent accurately. Bent sheet metal which has been cut with a laser cutting machine can have a tolerance of +/-0.1 mm.
How Much Does Sheet Metal Bending Cost?
Sheet metal bending costs will vary depending on the complexity of the sheet metal bending project. A major factor in the price is labor costs. An increase in labor due to unique designs will greatly increase the cost. Conversely, large orders that use an automated process will drive down the price per unit. Additionally, the quality of the bending will factor in the price. This is because if the part has a loose tolerance, the scrap rate is reduced.
Is Sheet Metal Bending Expensive Compared To Die Casting?
No, sheet metal bending is cheaper than die casting initially. This is because sheet metal bending has more standardized tools and takes less time to set up. However, die casting may be much cheaper for large production batches as once the cast is made, die casting can produce many identical parts quickly.
What Are the Advantages of Using CO2 Laser Cutting in Sheet Metal Bending?
The biggest advantage of using laser cutting for sheet metal bending is the accuracy with which it cuts. The improvement in the accuracy of cutting directly affects the accuracy of the bending. Other advantages of using laser cutting for sheet metal bending include:
- Increased speed due to automation.
- Reduced cost due to automation.
- Shorter lead times due to increased productivity.
To learn more, see our guide on CO2 Lasers.
What Are the Disadvantages of Using CO2 Laser Cutting Sheet in Sheet Metal Bending?
One drawback of using laser cutting with sheet metal bending is the large initial cost of a laser cutting machine. Although, this cost can be recuperated if there is enough work to use it effectively. Other disadvantages of using a laser cutting machine for sheet metal bending include:
- Laser cutting requires highly skilled labor which may not always be available.
- Increased risk of harmful fumes.
- High energy consumption to power the laser cutter.
What Are Examples of Sheet Metal Bending Products?
There are a wide variety of products made using sheet metal, including:
- Body panels for automotive, aerospace, and other vehicles.
- Electrical components.
- White goods (microwaves, fridges, washing machines, etc.).
- Gas cylinders.
What Is the Lifespan of Sheet Metal Bending Products?
The life span of sheet metal bending products will depend on many factors. However, the fact that the product is bent out of sheet metal will not be the limiting factor. Major factors that affect the life span include: strength, fatigue life, corrosion resistance, design suitability, operating environment, and maintenance of the product. With all of these factors to consider, the exact life span is very subjective. However most estimates for the life span of galvanized sheet metal range between 25–45 years.
What Is the Quality of Sheet Metal Bending Products?
The sheet metal bending process is recognized as producing high-quality parts. The exact quality will depend on: the design, material, manufacturer, and equipment used. However, the bending process is not the limiting factor in the quality of a sheet metal product.
Are Sheet Metal Bending Products Durable?
Yes, sheet metal parts are extremely durable. Sheet metal is especially durable when made out of a corrosion-resistant material such as stainless or galvanized steel. The continuous nature of sheet metal eliminates stress points, increasing a part’s longevity.
Summary
This article presented sheet metal bending, explained it, and discussed its purpose and advantages. To learn more about sheet metal bending, contact a Xometry representative.
Xometry provides a wide range of manufacturing capabilities, including sheet cutting and other value-added services for all of your prototyping and production needs. Visit our website to learn more or to request a free, no-obligation quote.
Disclaimer
The content appearing on this webpage is for informational purposes only. Xometry makes no representation or warranty of any kind, be it expressed or implied, as to the accuracy, completeness, or validity of the information. Any performance parameters, geometric tolerances, specific design features, quality and types of materials, or processes should not be inferred to represent what will be delivered by third-party suppliers or manufacturers through Xometry’s network. Buyers seeking quotes for parts are responsible for defining the specific requirements for those parts. Please refer to our terms and conditions for more information.
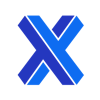